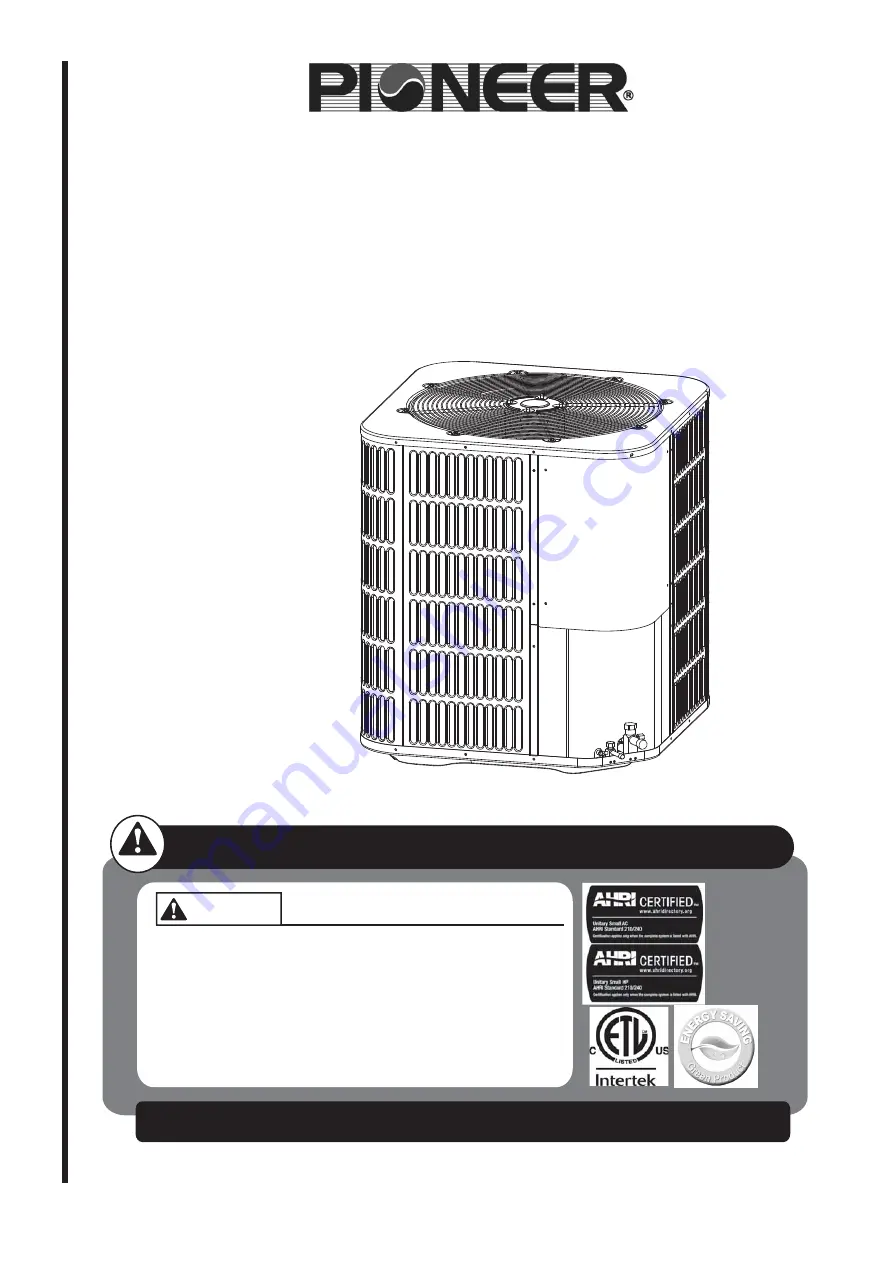
WARNING
These instructions are intended as an aid to qualified
licensed service personnel for proper installation, adjust-
ment and operation of this unit. Read these instructions
thoroughly before attempting installation or operation.
Failure to follow these instructions may result in improper
installation, adjustment, service or maintenance possibly
resulting in fire, electrical shock, property damage,
personal injury or death.
RECOGNIZE THIS SYMBOL AS AN INDICATION OF IMPORTANT SAFETY INFORMATION
DO NOT DESTROY THIS MANUAL
Please read carefully and keep in a safe place for future reference by a serviceman.
NOTE
: Appearance of unit may vary.
INSTALLATION INSTRUCTIONS
18 SEER
SEER
DC INVERTER
Split System Heat Pump & Air Conditioner
2-5 Tons
-
R410A
208~230 V. 1 Ph. 60 Hz.
Models:
YD024GMFI18MR2
YD036GMFI18MR2
YD048GMFI18MR2
YD060GMFI18MR2