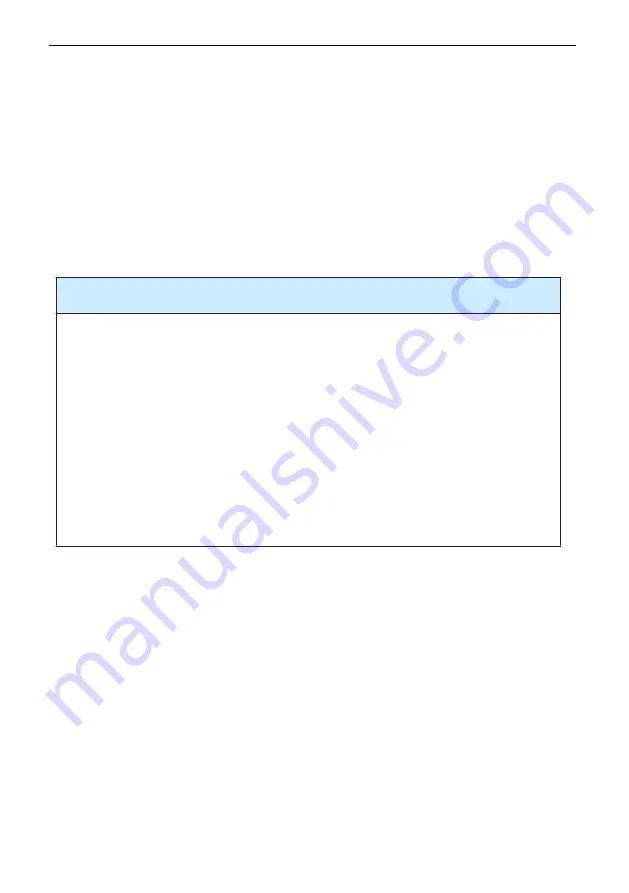
PE6000 User Manual Preface
1
Preface
Thank you for purchasing the PE6000 series AC drive
The PE6000 series AC drive is a general-purpose high-performance current vector control AC
drive. It is used to drive various automation production equipment involving textile, paper-making,
wiredrawing, machine tool, packing, food, fan and pump.
This manual describes the correct use of the PE6000 series AC drive, including selection,
parameter setting, commissioning, maintenance & inspection. Read and understand the manual
before use and forward the manual to the end user.
Notes
•
The drawings in the manual are sometimes shown without covers or protective
guards. Remember to install the covers or protective guards as specified first, and
then perform operations in accordance with the instructions.
•
The drawings in the manual are shown for description only and may not match the
product you purchased.
•
The instructions are subject to change, without notice, due to product upgrade,
specification modification as well as efforts to increase the accuracy and convenience of
the manual.
•
Contact our agents or customer service center if you have problems during the use. Phone
number:400-688-2700