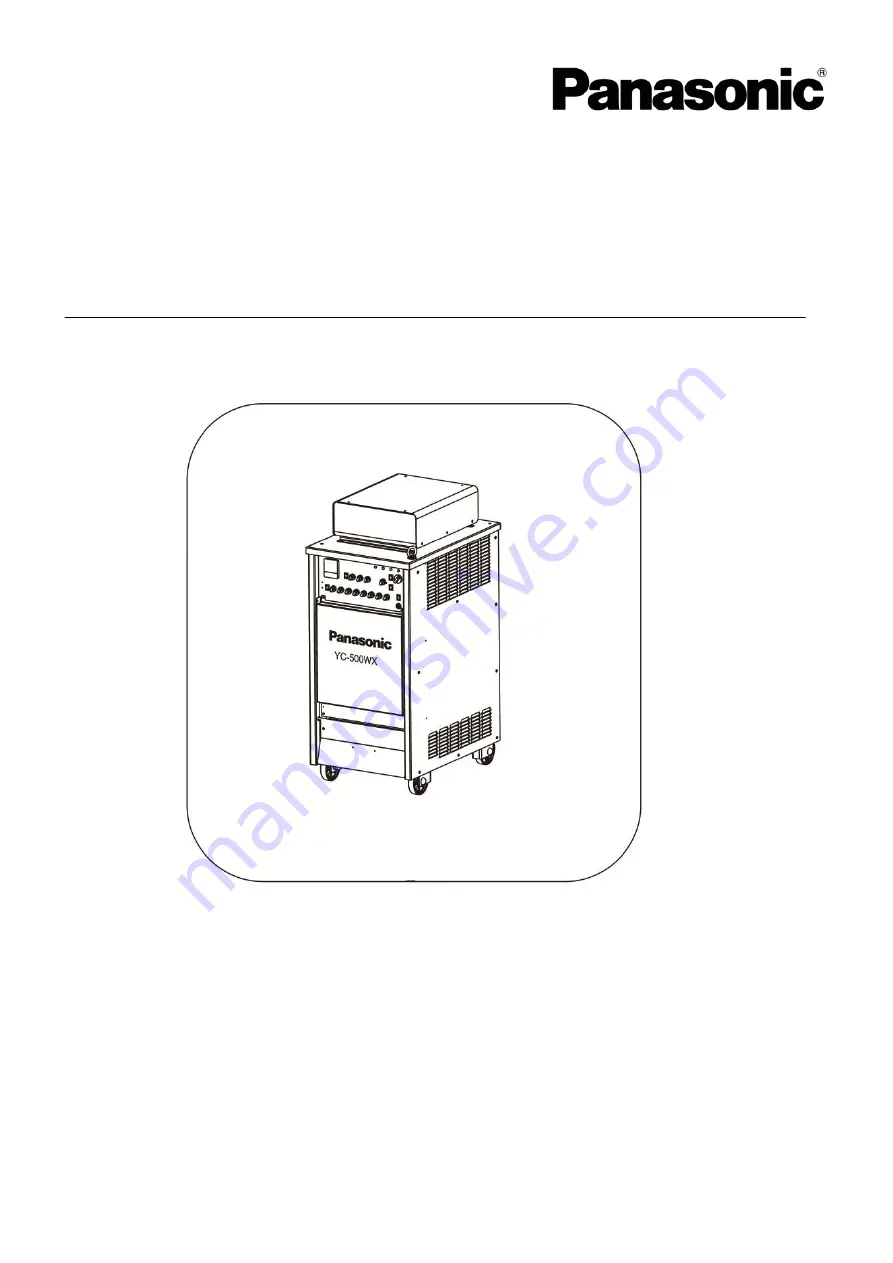
Operating Instructions
IGBT Controlled
AC/DCTIG arc welding power source
Model N o . :
YC-500 WX
`
●
Thank you for your purchase of Panasonic welding power source.
●
Before operating this product, please read the instructions carefully and save this manual
for future use.First of all
please read “Safety precautions” or “Safety manual”.
●
SPEC. No.
:
YC-500WX4HGX
Panasonic Welding Systems (Tangshan) Co., Ltd.
WTC017TEOPAA02
Summary of Contents for YC-500WX
Page 2: ......
Page 20: ...13 ...
Page 21: ...14 ...
Page 30: ...23 12 CIRCUITDIAGRAM ...
Page 31: ...24 13 PARTS LAYOUT DRAWING ...
Page 34: ...27 15 OUTLING DRAWING ...