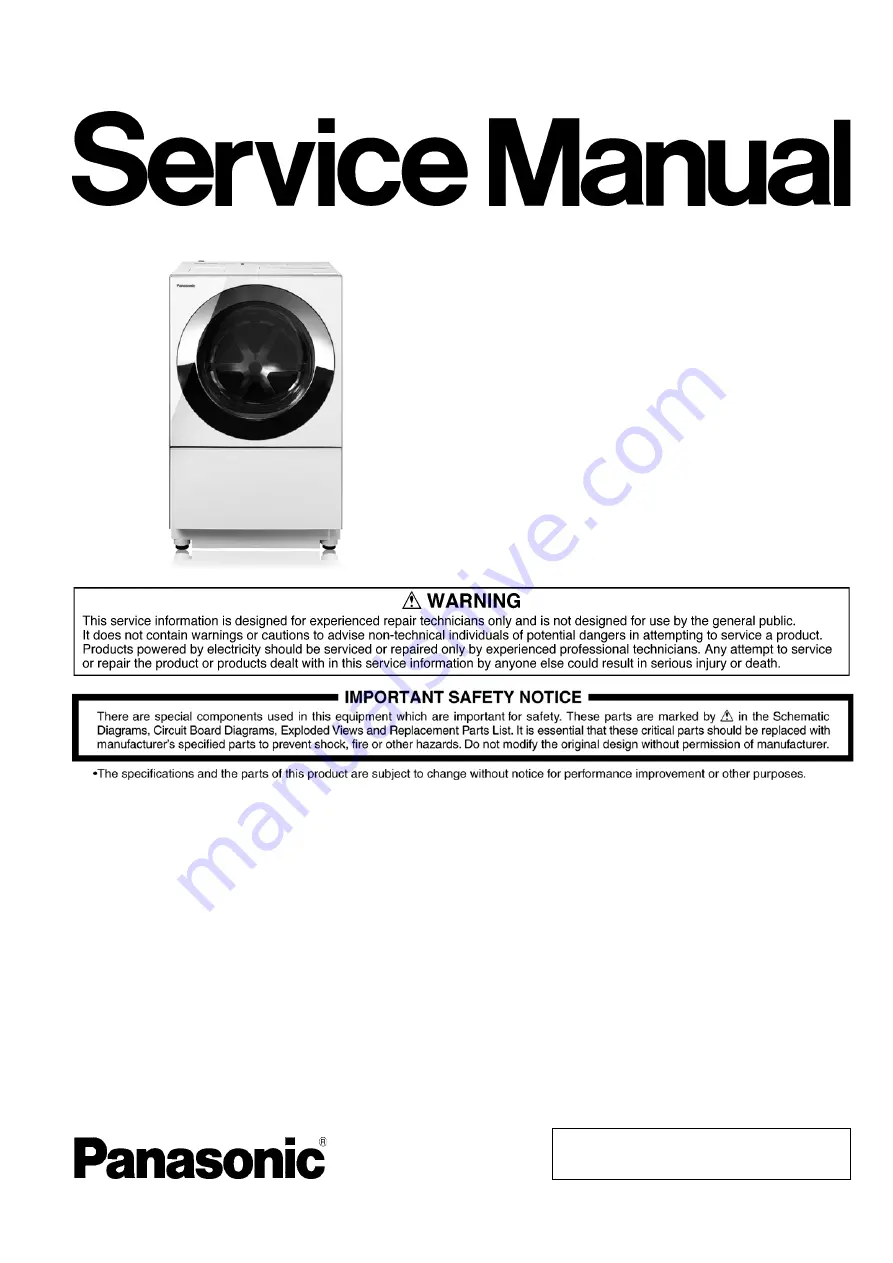
© Panasonic Corporation 2016 Unauthorized copy-
ing and distribution is a violation of law.
Order No.APJWM160401CE
Washer Dryer
Model No.
NA-D106X1
Product Color :White
Destination :Malaysia, Singapore, Thailand, Philippines
TABLE OF CONTENTS
PAGE
PAGE
1 Safety Precautions
-----------------------------------------------
2 Specifications
-----------------------------------------------------
3 General/Introduction
--------------------------------------------
4 Control panel
------------------------------------------------------
5 Feature and Technical Description
-------------------------
6 Installation Instructions
----------------------------------------
7 Operating Instructions
-----------------------------------------
8 Disassembly Instructions and Adjustments
-----------
9 Wiring Diagram (OUTLINE) Drawing
----------------------
10 Troubleshooting Guide
----------------------------------------
11 External Diameter
-----------------------------------------------
12 Exploded View and Replacement Parts List
-----------
Summary of Contents for NA-D106X1
Page 2: ...2 NA D106X1 1 Safety Precautions ...
Page 4: ...4 NA D106X1 3 General Introduction 3 1 Location of Components and Accessories ...
Page 5: ...5 NA D106X1 4 Control panel ...
Page 7: ...7 NA D106X1 5 3 Active Foam system 5 4 ECONAVI ...
Page 8: ...8 NA D106X1 5 5 Eco Drying system ...
Page 9: ...9 NA D106X1 6 Installation Instructions ...
Page 10: ...10 NA D106X1 ...
Page 11: ...11 NA D106X1 ...
Page 12: ...12 NA D106X1 ...
Page 13: ...13 NA D106X1 7 Operating Instructions 7 1 Door Lock and Child Lock ...
Page 14: ...14 NA D106X1 7 2 Laundry Procedure ...
Page 15: ...15 NA D106X1 7 3 Selecting the Program ...
Page 16: ...16 NA D106X1 7 4 How to Put in Detergent and Sofetner ...
Page 17: ...17 NA D106X1 7 5 Everyday Washing ...
Page 18: ...18 NA D106X1 7 6 Washing Options ...
Page 19: ...19 NA D106X1 ...
Page 20: ...20 NA D106X1 7 7 Drying ...
Page 21: ...21 NA D106X1 7 8 Maintenance ...
Page 22: ...22 NA D106X1 ...
Page 23: ...23 NA D106X1 7 9 Changing the Settings ...
Page 24: ...24 NA D106X1 7 10 Program Details ...
Page 46: ...46 NA D106X1 9 Wiring Diagram OUTLINE Drawing 9 1 NA D106X1 Wiring Diagram ...
Page 47: ...47 NA D106X1 9 2 Measure Input and Output value of Controller Power side ...
Page 56: ...56 NA D106X1 11 External Diameter ...
Page 57: ...57 NA D106X1 ...
Page 58: ...58 NA D106X1 12 Exploded View and Replacement Parts List 12 1 Parts Exploded View Part A ...
Page 60: ...60 NA D106X1 12 3 Parts Exploded View Part B ...
Page 62: ...62 NA D106X1 12 5 Parts Exploded View Part C ...
Page 64: ...64 NA D106X1 12 7 Parts Exploded View Part D ...
Page 66: ...66 NA D106X1 12 9 Parts Exploded View Part E ...