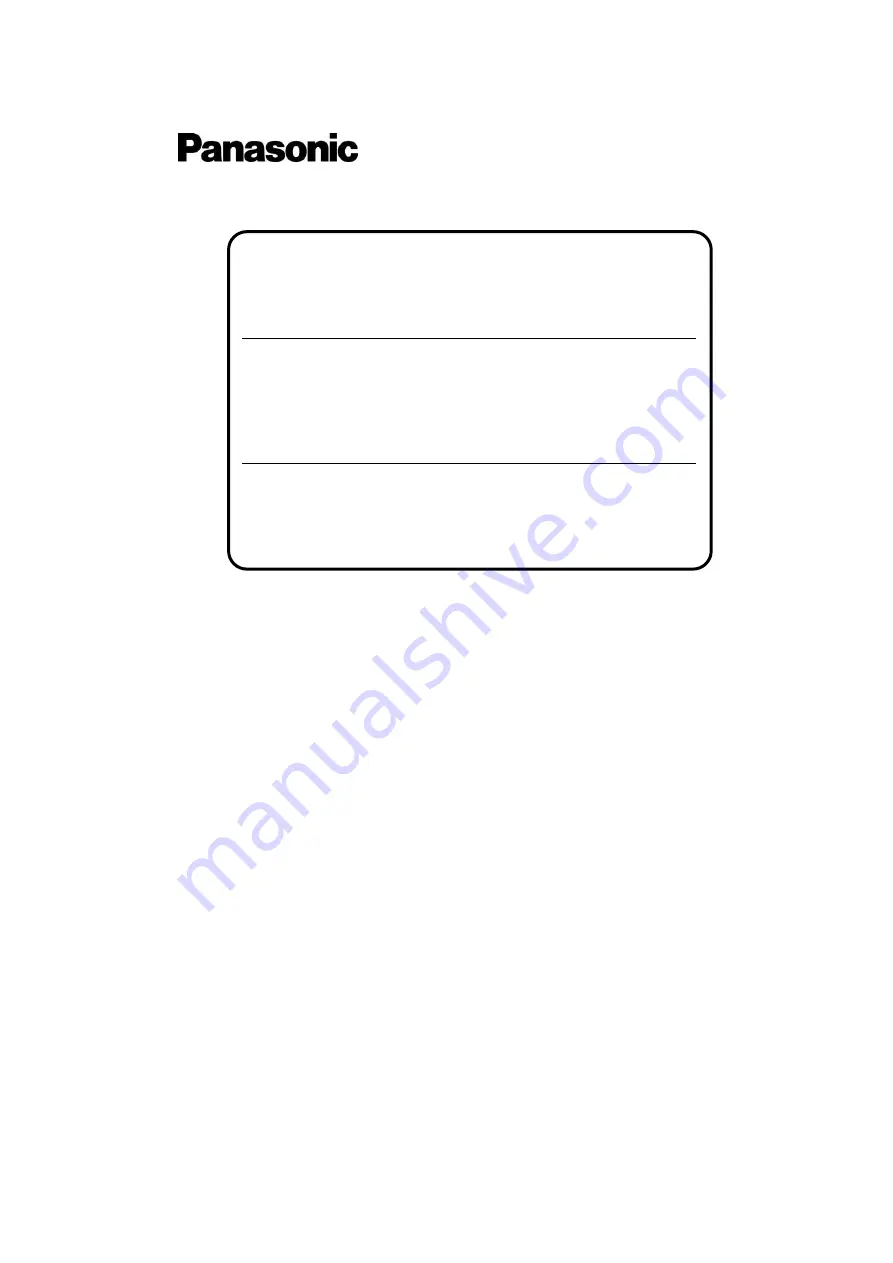
R1.7
No. SX-DSV03455
TECHNICAL REFERENCE
– Functional Specification –
MODEL
Product Name
: AC Servo Driver
Product No.
: MINAS A6 Multi series
(EtherCAT communication/rotation type)
Issued on
Jun. 16, 2020
Revised on
Industrial Device Solution Business Unit, Industrial Device Business Division,
Industrial Solutions Company, Panasonic Corporation
7-1-1 Morofuku, Daito-City, Osaka 574-0044, Japan
Phone
: +81-72-871-1212
Fax : +81-72-870-3151
Summary of Contents for MINAS A6 Series
Page 10: ...Table of contents x Blank page...
Page 11: ...1 Introduction...
Page 26: ...Introduction 1 16 Blank page...
Page 27: ...2 Interface Specifications...
Page 46: ...Interface Specifications 2 20 Blank page...
Page 47: ...3 Front Panel Specifications...
Page 57: ...4 Basic Functions...
Page 85: ...5 Auto Tuning Functions...
Page 151: ...6 Application Functions...
Page 185: ...7 Protective Functions...
Page 224: ...Protective Functions 7 40 Blank page...
Page 225: ...8 Advanced Safety Functions...
Page 230: ...Advanced Safety Functions 8 6 When test pulse is used Duplex safety input Safety input...
Page 245: ...9 List of Parameters...
Page 281: ...10 Timing Chart...
Page 290: ...Timing Chart 10 10 Blank page...
Page 291: ...11 Power Supply Module...