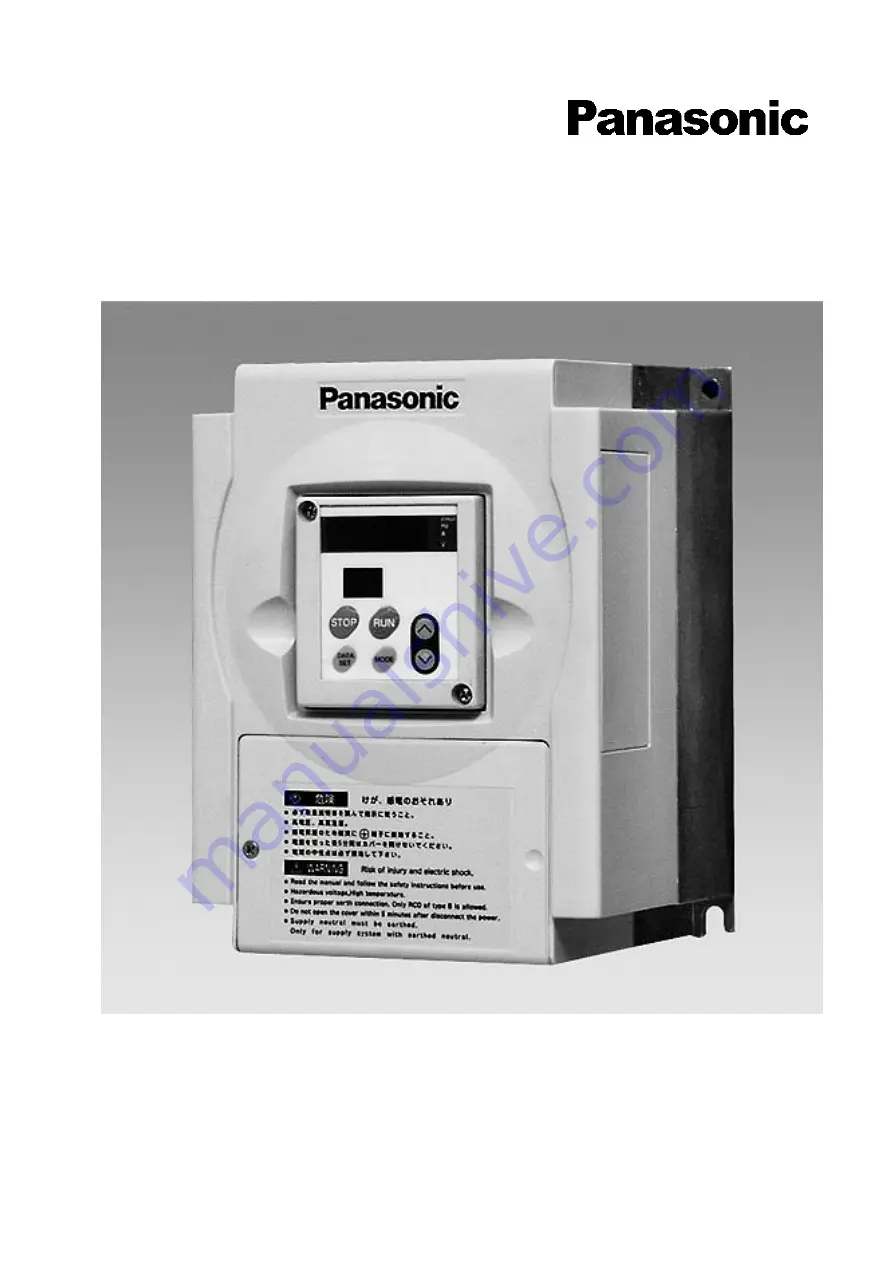
M2X Series Inverter
for
3-phase Induction Motor Speed Control
INSTRUCTION MANUAL
Be sure to hand over this instruction manual to customers.
●
Thank you for purchasing Panasonic Inverter.
●
To ensure proper use of this product, read this instruction manual
thoroughly.
Keep this manual in place, and read it whenever required.