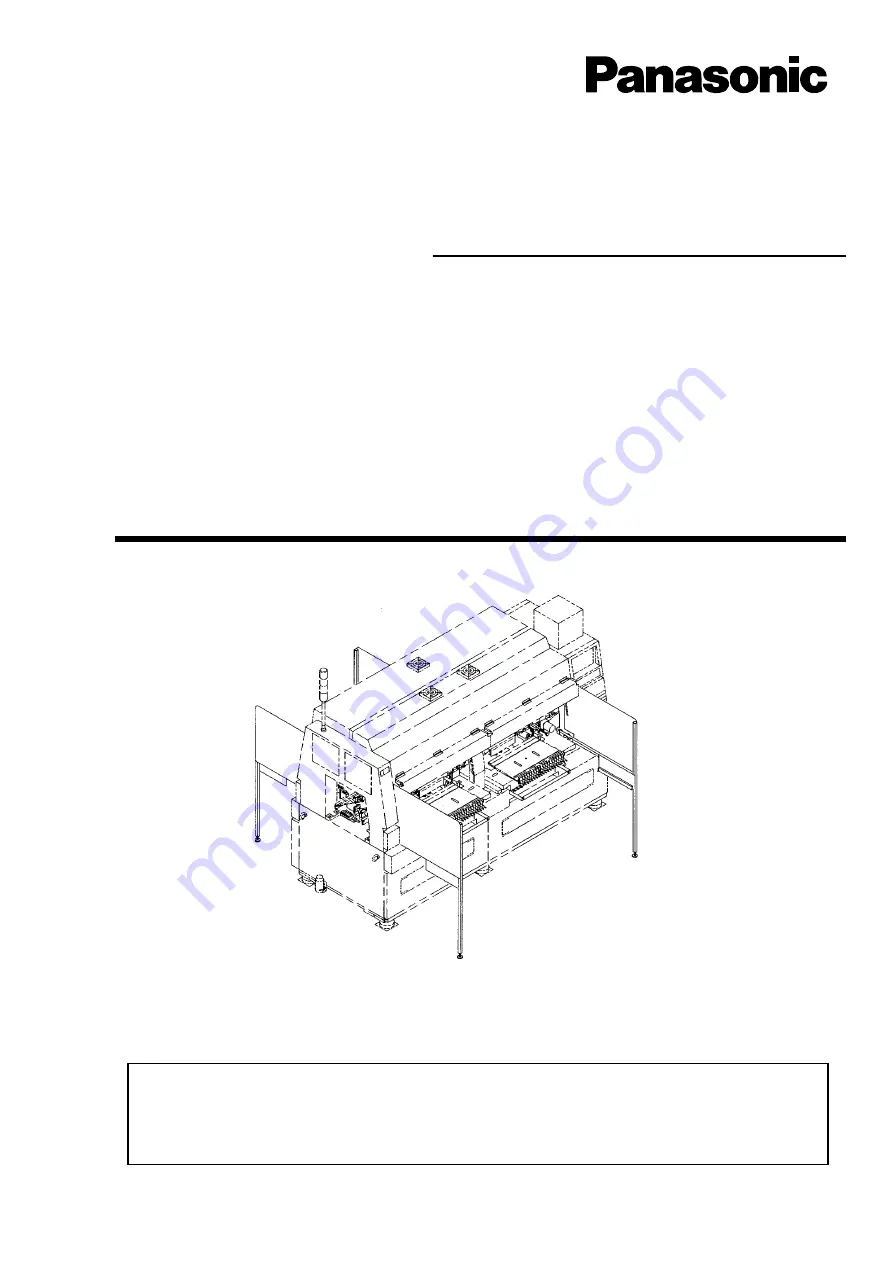
Operating Instructions
Model No.
KXF-3V3C
Thank you for purchasing CM95R, the multi-functional chip mounter.
Before placing the machine in service, be sure to read the instruction manual for
proper usage.
After that, store it carefully and it if necessary.
3V3C-E-MMDB-0001
Multi-functional Chip Mounter CM95R
Maintenance Manual
(1/2)
Summary of Contents for KXF-3V3C
Page 2: ......
Page 16: ...Page 16 CONTENTS 3V3C E MMD00 A03 01 MEMO ...
Page 38: ...3V3C E MMD00 A08 01 MEMO ...
Page 214: ...MAINTENANCE Section 2 ERROR MESSAGES Page 2 106 Multi tray Feeder 3V3C E MMD02 A04 01 MEMO ...
Page 365: ...I N D E X I N D E X I N D E X 3V3C E MMD00 A08 00 ...
Page 366: ...3V3C E MMD00 A08 01 MEMO ...