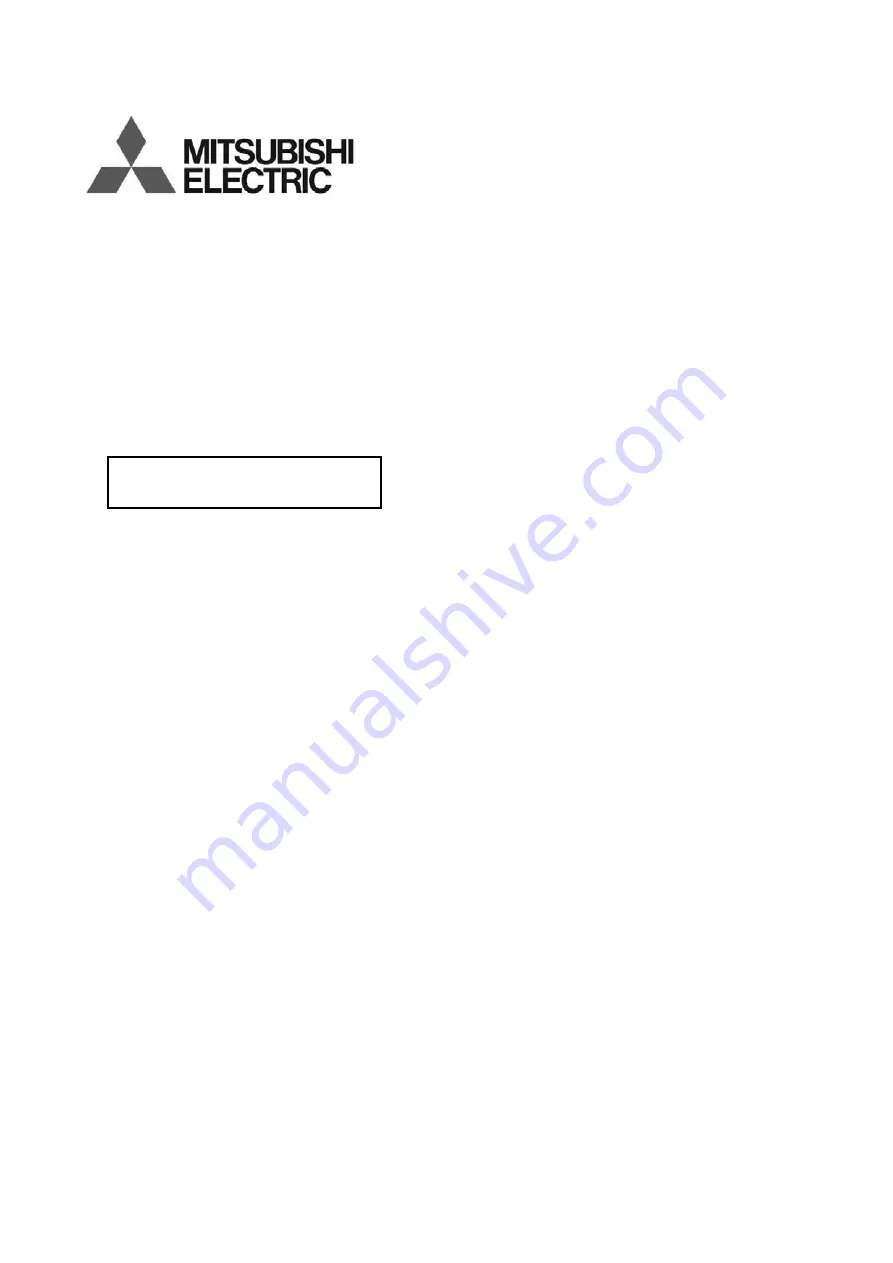
MITSUBISHI HOIST
Type UM (5t , 10t)
INSTRUCTION MANUAL
☆
Be sure to hand this instruction manual to the person in charge of facilities before starting
operation.
☆
Be sure to have the person in charge of facilities and operators read this manual thoroughly before
starting operation.
Instruction Manual PHN14A003
-
A
Standard Version
Summary of Contents for UM 10t
Page 51: ... 47 Structural Drawing of Hoist Main Body 5t 10t PA00531 ...
Page 52: ... 48 Structural Drawing of Electric Traversing Unit Monorail Type 10t P288922 ...
Page 53: ... 49 Structural Drawing of Electric Traversing Unit Double rail type 5t PA00483 ...
Page 54: ... 50 Structural Drawing of Traversing Mortor Double rail type 10t P276926 ...
Page 55: ... 51 Structural Drawing of Hook Block 5t PG49975 ...
Page 56: ... 52 Structural Drawing of Hook Block 10t PG49976 ...