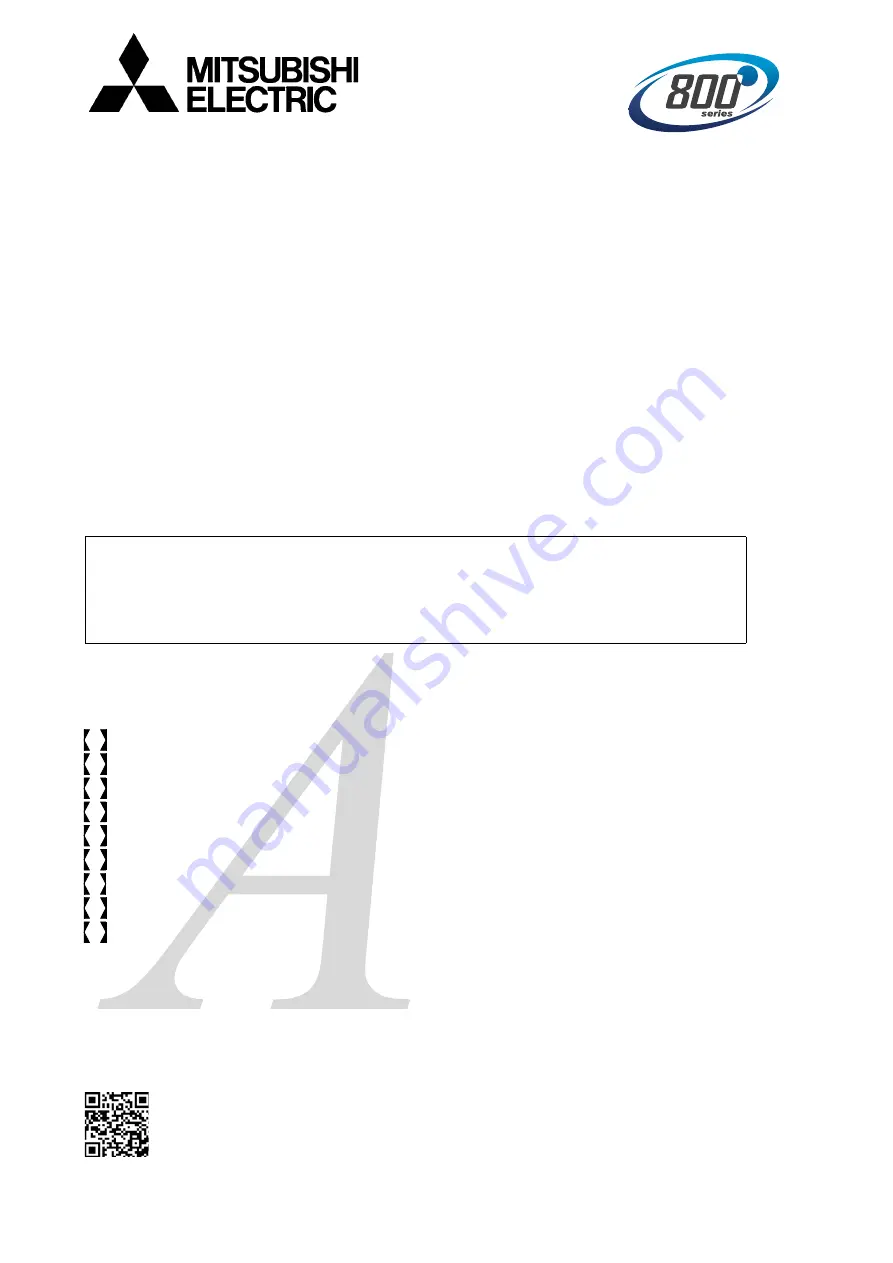
INVERTER
FR-A800
INSTALLATION GUIDELINE
FR-A820-00046(0.4K) to 04750(90K)
FR-A840-00023(0.4K) to 06830(280K)
FR-A842-07700(315K) to 12120(500K)
FR-A846-00023(0.4K) to 00470(18.5K)
800
CONTENTS
INSTALLATION AND INSTRUCTIONS..................................................................... 1
FAILSAFE OF THE SYSTEM WHICH USES THE INVERTER............................... 28
PRECAUTIONS FOR USE OF THE INVERTER ..................................................... 29
Thank you for choosing this Mitsubishi Inverter.
This Installation guideline and the enclosed CD-ROM give handling information and precautions for use
of this product.
Do not use this product until you have a full knowledge of the equipment, the safety information and the
instructions.
Please forward this Installation guideline and the CD ROM to the end user.
A
Version check
Art. No.: 274662
19 08 2014
Version D
Summary of Contents for FR-A800
Page 67: ......