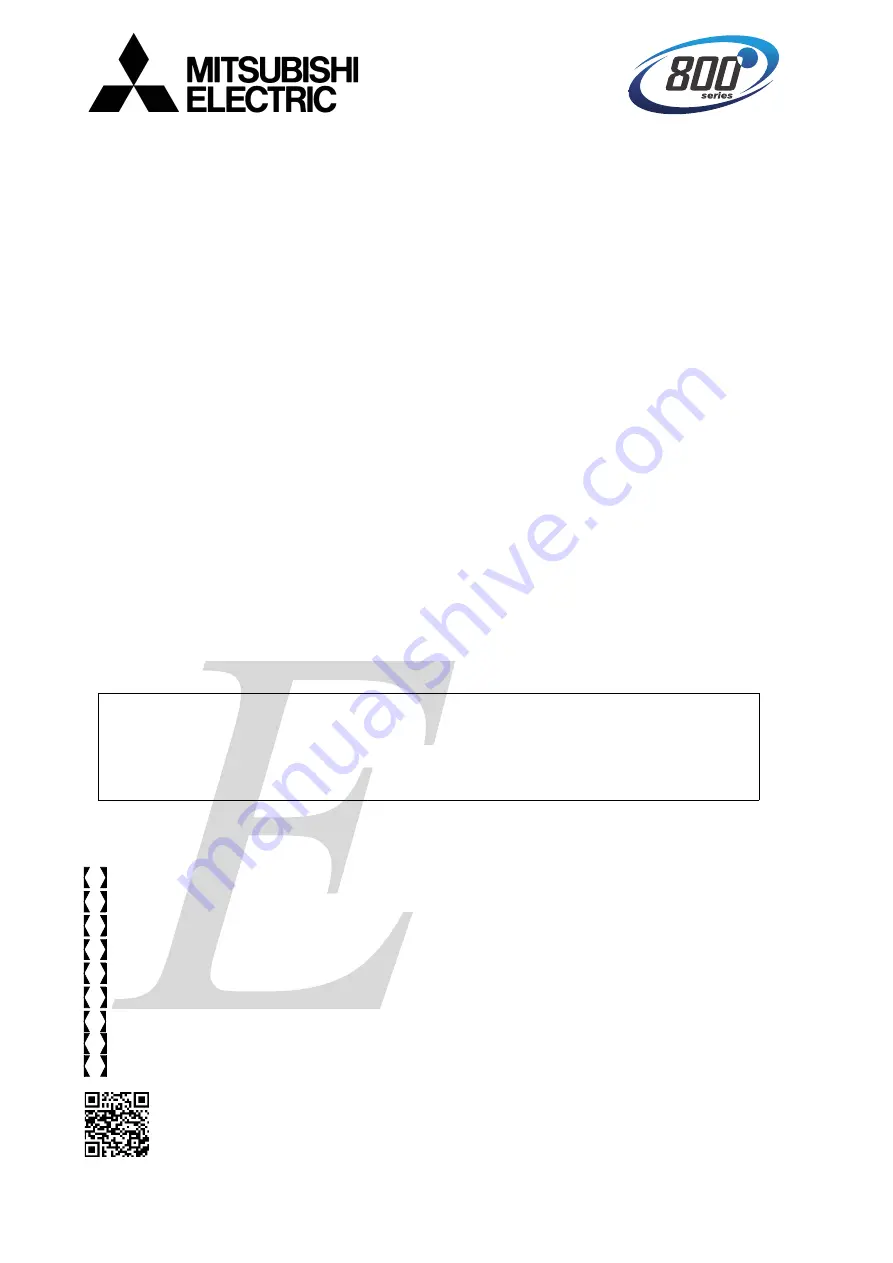
INVERTER
FR-E800
INSTALLATION GUIDELINE
FR-E820-0008(0.1K) to 0900(22K)
FR-E840-0016(0.4K) to 0440(22K)
FR-E820S-0008(0.1K) to 0110(2.2K)
FR-E820-0008(0.1K)E to 0900(22K)E
FR-E840-0016(0.4K)E to 0440(22K)E
FR-E820S-0008(0.1K)E to 0110(2.2K)E
FR-E820-0008(0.1K)SCE to 0900(22K)SCE
FR-E840-0016(0.4K)SCE to 0440(22K)SCE
FR-E820S-0008(0.1K)SCE to 0110(2.2K)SCE
CONTENTS
INSTALLATION AND INSTRUCTIONS.....................................................................1
WIRING ...................................................................................................................... 5
FAILSAFE OF THE SYSTEM WHICH USES THE INVERTER............................... 31
PRECAUTIONS FOR USE OF THE INVERTER ..................................................... 29
BASIC OPERATION ................................................................................................ 35
PARAMETER LIST .................................................................................................. 41
INVERTER FAULT AND ALARM INDICATIONS.................................................... 55
SPECIFICATIONS ................................................................................................... 59
APPENDIX .............................................................................................................. 65
Thank you for choosing this Mitsubishi Electric Inverter.
This Installation guideline and the enclosed CD-ROM give handling information and precautions for use
of this product.
Do not use this product until you have a full knowledge of the equipment, the safety information and the
instructions.
Please forward this Installation guideline to the end user.
A
Version check
Art. no.: 574333
25082021
Version B
Summary of Contents for 800 Series
Page 10: ...4 INSTALLATION AND INSTRUCTIONS ...
Page 46: ...40 BASIC OPERATION ...
Page 64: ...58 INVERTER FAULT AND ALARM INDICATIONS ...
Page 70: ...64 SPECIFICATIONS ...