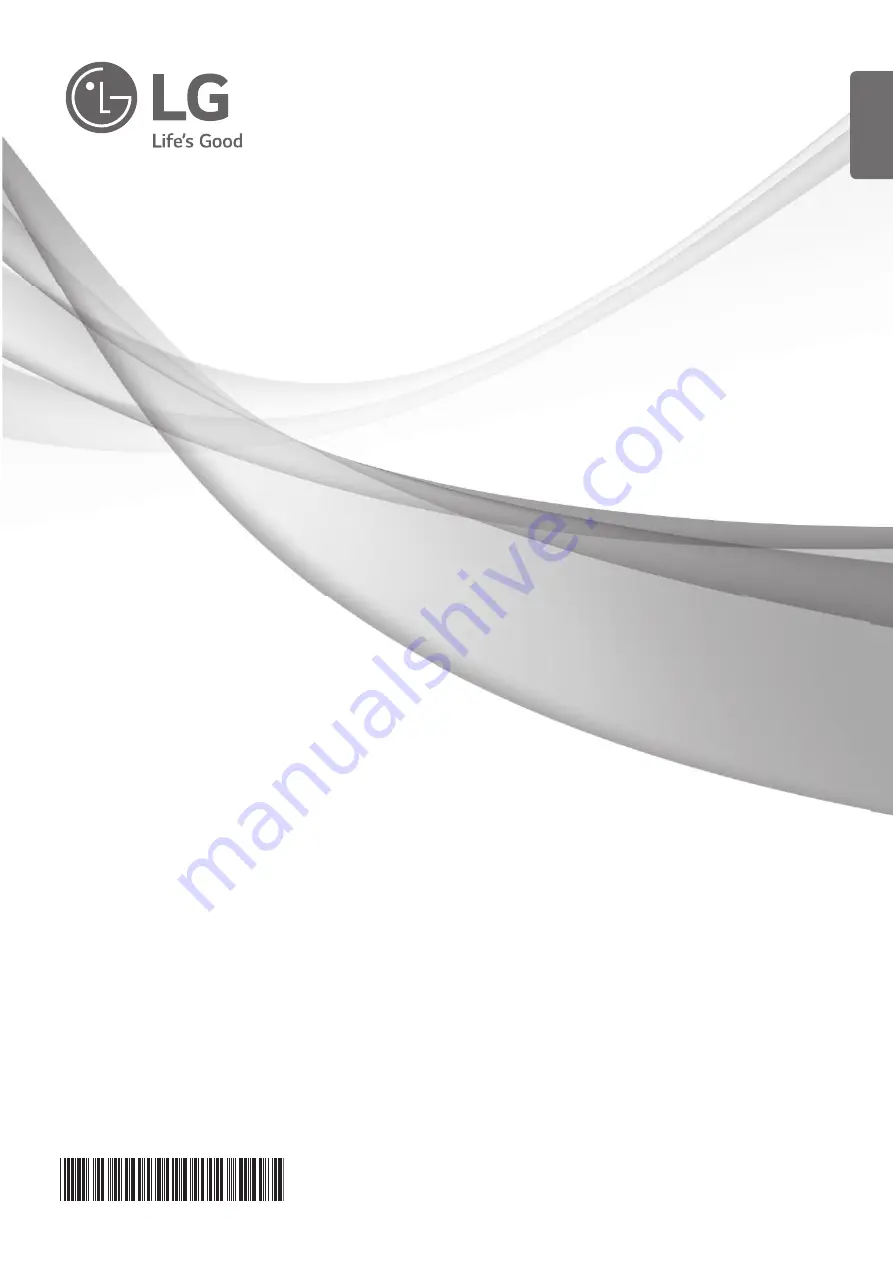
www.lge.com
INSTRUCTION MANUAL
Water-Cooled Turbo Chiller
Please read the safety precautions before use.
This content is to ensure the safety of users and to prevent property damages.
Keep the instruction manual in a place that is accessible to other users.
Only authorized people can use the product.
Model : RCWFH Series (200-3000RT)
(For AC Smart Premium Control System)
ENGLISH
P/NO : MFL68929306
(Rev 0)