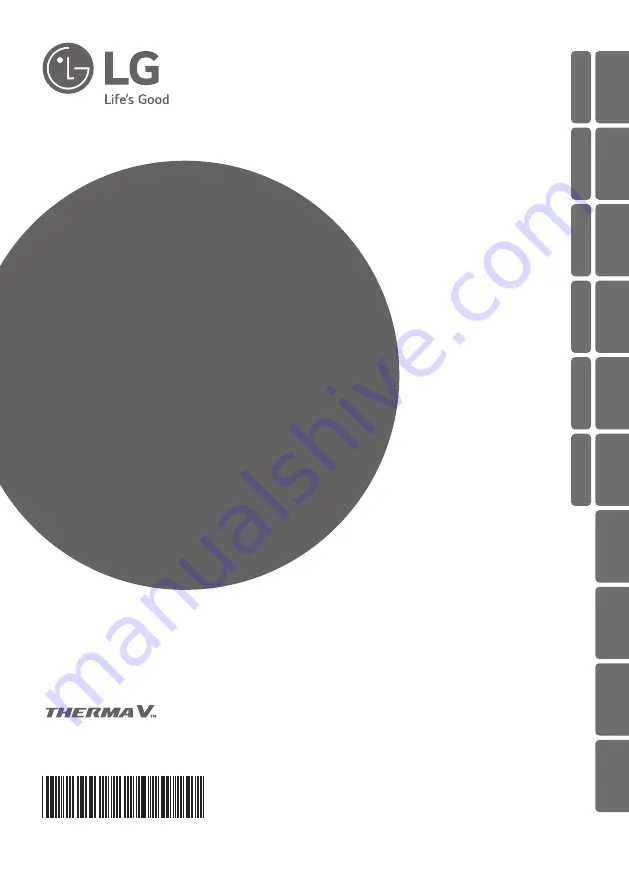
INSTALLATION MANUAL
AIR-TO-WATER
HEAT PUMP
www.lg.com
Please read this installation manual completely before installing the
product. Installation work must be performed in accordance with the
national wiring standards by authorized personnel only. Please retain
this installation manual for future reference after reading it thoroughly.
Original instruction
Copyright © 2020 LG Electronics Inc. All Rights Reserved.
MFL68681818
Rev.00_070220
ENGLISH
ITALIANO
ESPAÑOL
FRANÇAIS
DEUTSCH
ΕΛΛΗΝΙΚΆ
ČEŠTINA
NEDERLANDS
POLSKI
LIMBA ROMÂNĂ
PORTUGUÊS
MAGYAR
БЪЛГАРСКИ
SRPSKI
HRVATSKI
SLOVENŠČINA