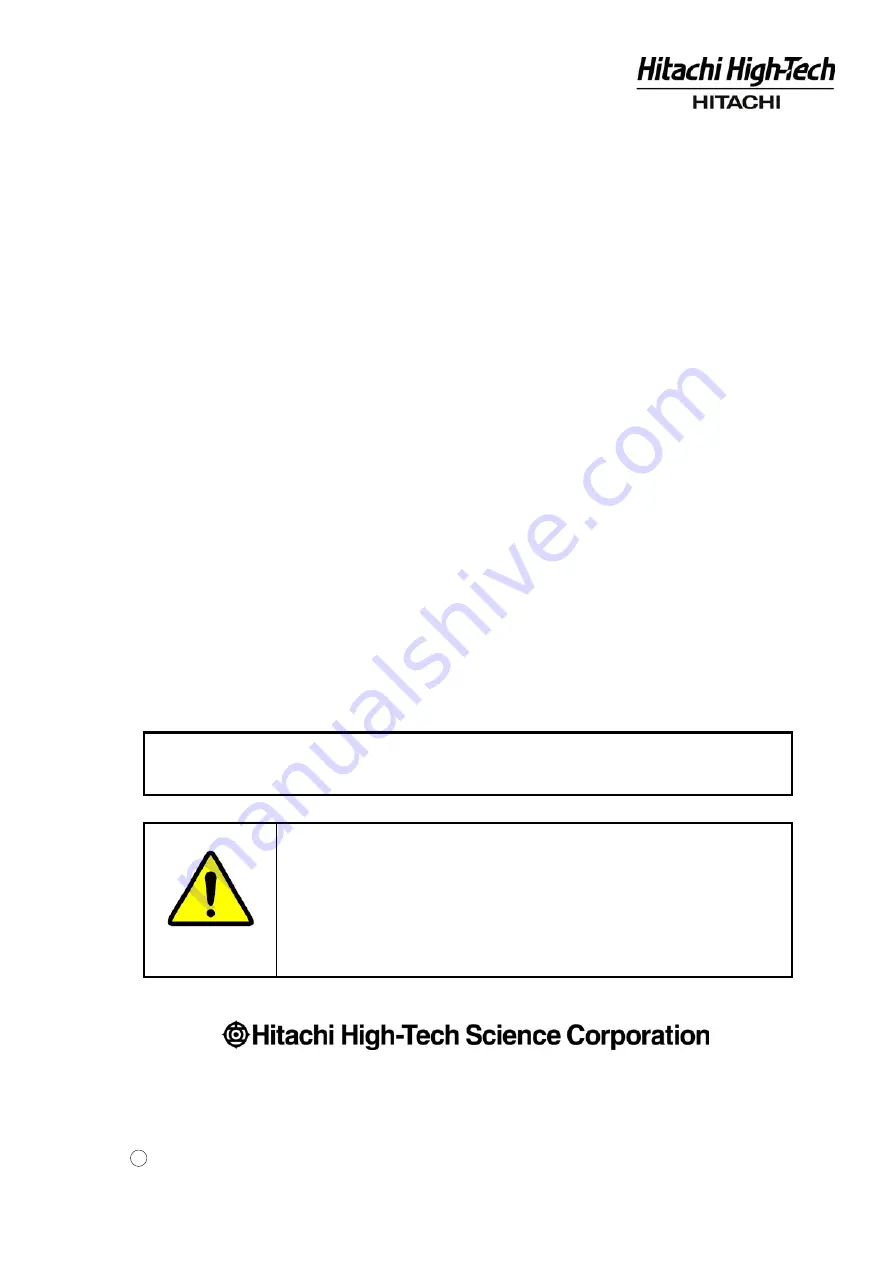
INSTRUCTION MANUAL
FOR
CHROMASTER 5160 PUMP
This product is intended for research use only. It is not to be used for reporting
patient diagnostic or therapeutic results.
Before using the instrument, read the safety instructions and
precautions carefully.
Be sure to observe the safety instructions in this manual and
the WARNING/CAUTION labels on the instrument.
Keep this manual in a safe place nearby so it can be referred
to whenever needed.
24-14, Nishi-Shimbashi 1-chome, Minato-ku, Tokyo, Japan
3rd Edition, August 2014
Copyright C Hitachi High-Tech Science Corporation 2013.
1st Edition, 2012
All rights reserved. Printed in Japan.
Part No. 892-9162-2
Summary of Contents for CHROMASTER 5160
Page 244: ......
Page 406: ......
Page 999: ...Retaining screws Fixing bracket Appended Fig 1 5 Removal of Fixing Brackets APPENDIX 1 13 ...
Page 1016: ......