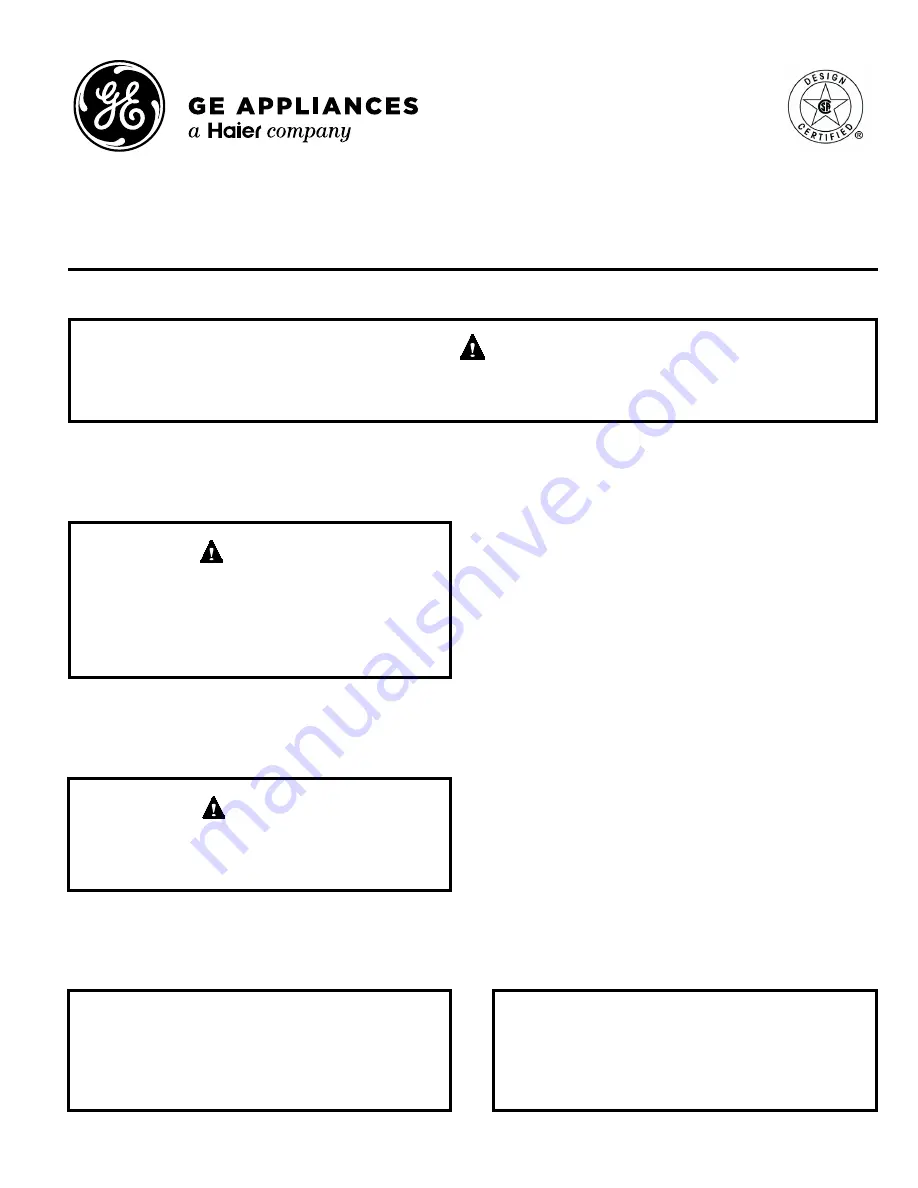
507332-02G / 31-5000663
Page 1 of 35
Issue 2209
(P) 507332-02G
*P507332-02G*
GE Appliances
A Haier Company
Appliance Park
Louisville, KY 40225
This manual must be left with the homeowner for future reference.
This is a safety alert symbol and should never be ignored. When you see this symbol on labels or in manuals, be alert to
the potential for personal injury or death.
Improper installation, adjustment, alteration, service
or maintenance can cause property damage, personal
injury or loss of life. Installation and service must be
performed by a licensed professional installer (or
equivalent), service agency or the gas supplier.
WARNING
As with any mechanical equipment, personal injury can
result from contact with sharp sheet metal edges. Be
careful when you handle this equipment.
CAUTION
Table of Contents
Unit Dimensions ..........................................................2
Parts Arrangement.......................................................3
Gas Furnace ................................................................4
Shipping and Packing List ...........................................4
Safety Information .......................................................4
General ........................................................................6
Combustion, Dilution & Ventilation Air .........................6
Setting Equipment .......................................................8
Filters .........................................................................11
Duct System ..............................................................11
Gas Piping .................................................................19
Electrical ....................................................................21
Unit Start-Up ..............................................................26
Blower Performance ..................................................30
Service.......................................................................32
Planned Service ........................................................34
Repair Parts List ........................................................34
INSTALLATION INSTRUCTIONS
NF80DS
Warm Air Gas Furnace
Downflow Air Discharge