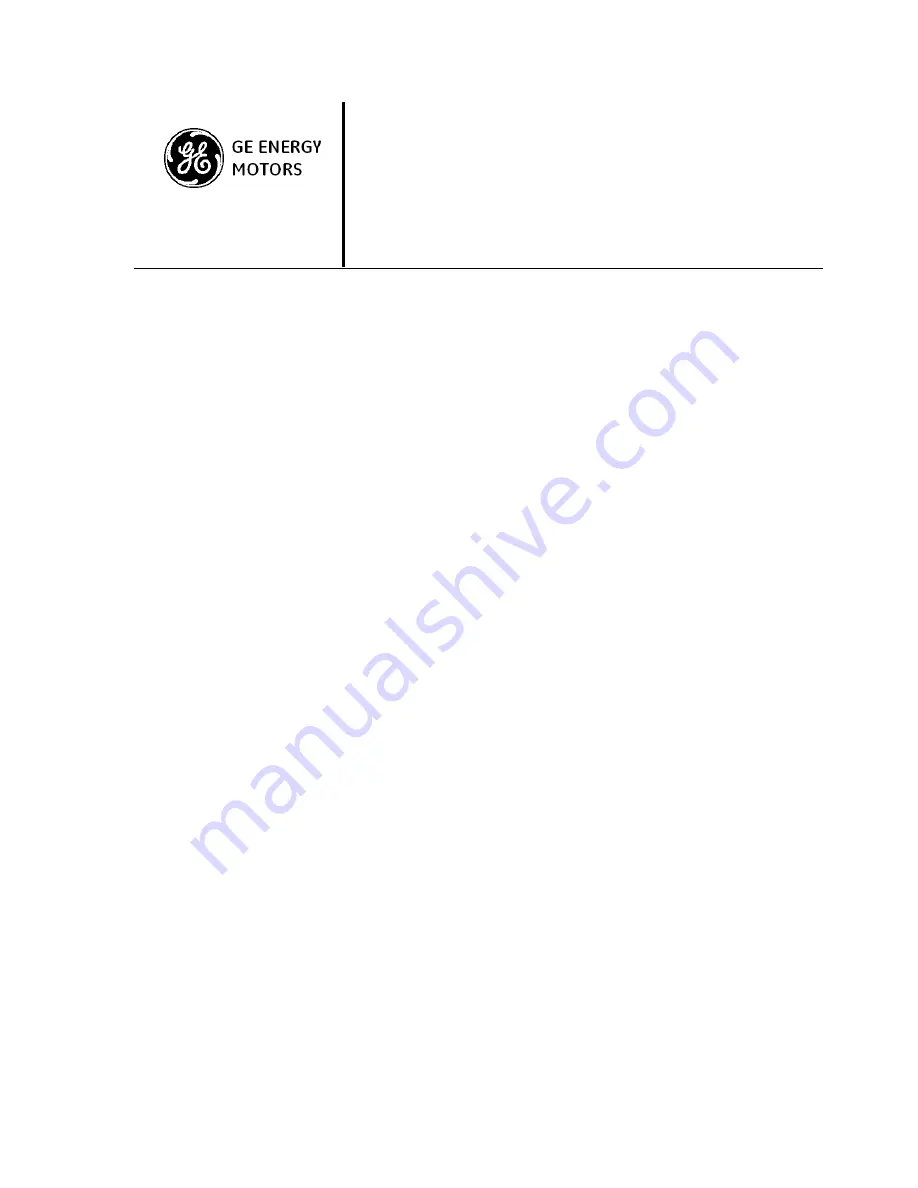
GEEP- 427-I
These Instructions do not purport to cover all details or variations in equipment nor to provide for every possible contingency to be met in connection with
installation, operation or maintenance. Should further information be desired or should particular problems arise which are not covered sufficiently for the
purchaser’s purposes, the matter should be referred to GE Energy Motors.
Pegasus MHV
®
is a registered trademark of General Electric Company.
GE Energy Motors GEEP-427-I Copyright 2009 The General Electric Company, USA 1
Instructions
Pegasus MHV
®
Horizontal
Induction Motor
Totally Enclosed Water-to-Air Cooled
Sleeve Bearing
Summary of Contents for Pegasus MHV GEEP-427-I
Page 46: ...GE Energy Motors 46 ...