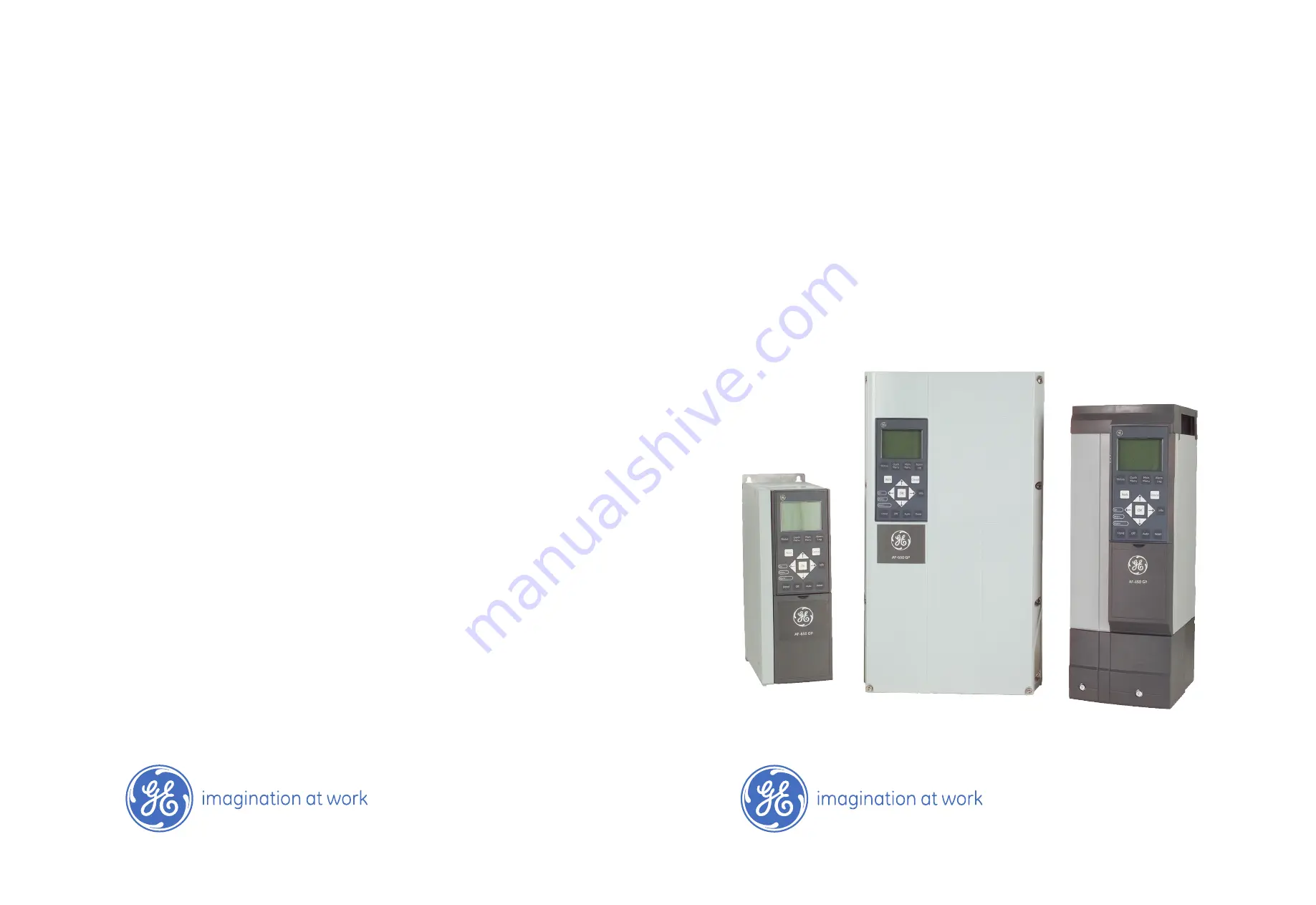
GE Consumer & Industrial
Electrical Distribution
AF-650 GP
TM
General Purpose Drive
Desi
gn Guide
The instructions do not purport to cover all details or variations in equipment nor to provide for every possible
contingency to be met in connection with installation, operation or maintenance. Should further information be
desired or should particular problems arise which are not covered sufficiently for the purchaser’s purposes, the
matter should be referred to the GE company.
AF-650 GP is a trademark of the General Electric Company.
GE Consumer & Industrial
41 Woodford Avenue
Plainville, CT 06062
www.geelectrical.com/drives
130R0361
*MG34H102*
DET-618
Summary of Contents for AF-650 GP Series
Page 5: ...AF 650 GP Design Guide 4 1...
Page 53: ...AF 650 GP Design Guide 52 4...
Page 97: ...Please note airflow directions 6 1 5 Mechanical Dimensions AF 650 GP Design Guide 96 6...
Page 98: ...Please note airflow directions AF 650 GP Design Guide 97 6...
Page 99: ...Please note airflow directions AF 650 GP Design Guide 98 6...
Page 100: ...Please note airflow directions AF 650 GP Design Guide 99 6...
Page 173: ...Max cable length 150 m AF 650 GP Design Guide 172 9...
Page 179: ...AF 650 GP Design Guide 178 9...