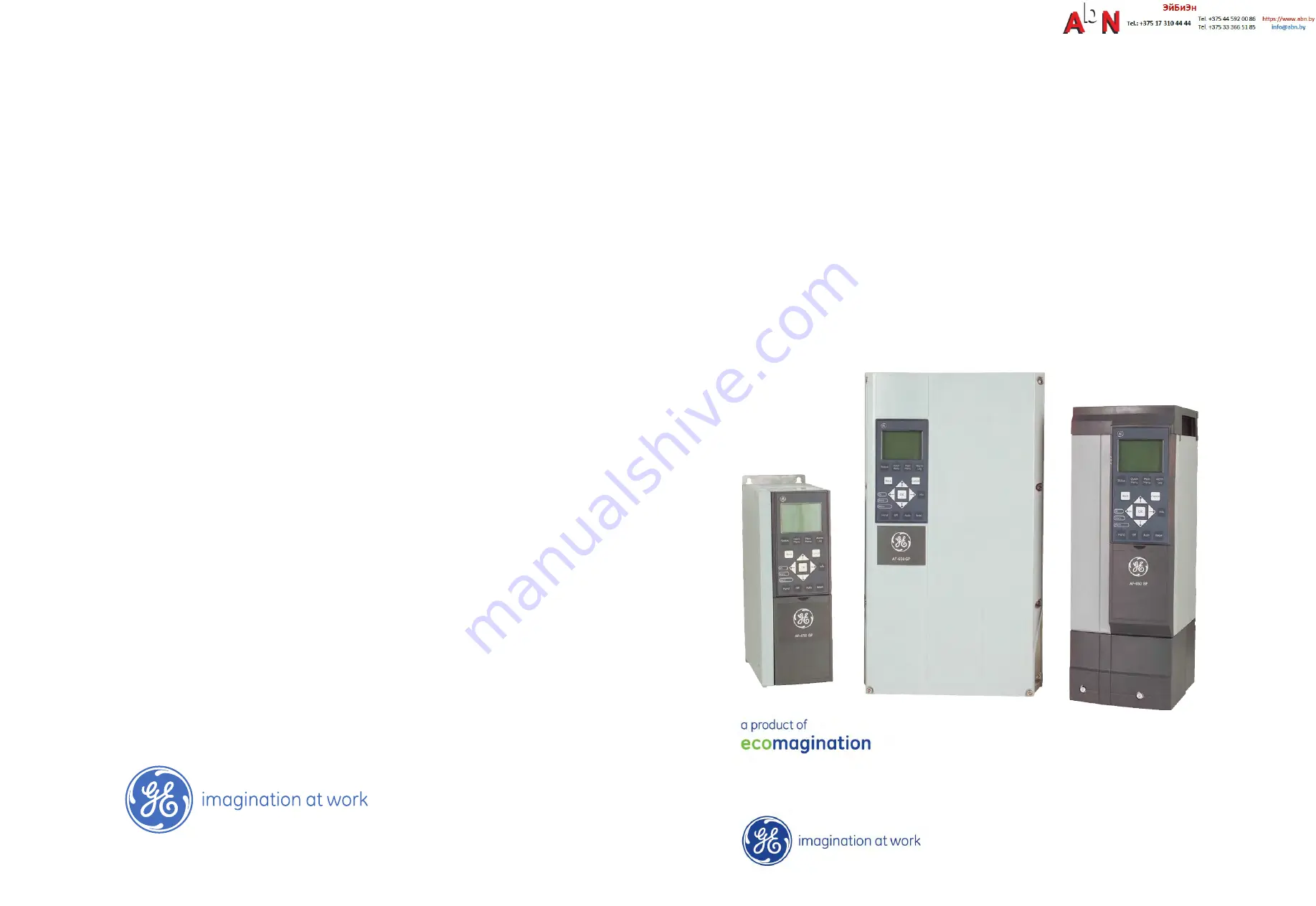
AF-650 GP
TM
General Purpose Drive
Design and Installation Guide
The instructions do not purport to cover all details or variations in equipment nor to provide for every possible
contingency to be met in connection with installation, operation or maintenance. Should further information be
desired or should particular problems arise which are not covered sufficiently for the purchaser’s purposes, the
matter should be referred to the GE company.
AF-650 GP is a trademark of the General Electric Company.
GE
41 Woodford Avenue
Plainville, CT 06062
www.geelectrical.com/drives
130R0415
*MG35M122*
DET-767A
GE
Summary of Contents for AF-650 GP Series
Page 3: ...Safety AF 650 GPTM Design and Installation Guide DET 767A ...
Page 9: ...Contents AF 650 GPTM Design and Installation Guide DET 767A ...
Page 19: ...Introduction AF 650 GPTM Design and Installation Guide 1 10 DET 767A 1 1 ...
Page 35: ...Installation AF 650 GPTM Design and Installation Guide 2 16 DET 767A 2 2 ...
Page 41: ...Start Up and Functional Tes AF 650 GPTM Design and Installation Guide 3 6 DET 767A 3 3 ...
Page 55: ...About Programming AF 650 GPTM Design and Installation Guide 5 10 DET 767A 5 5 ...
Page 91: ...Application Setup Examples AF 650 GPTM Design and Installation Guide 6 36 DET 767A 6 6 ...
Page 103: ...Status Messages AF 650 GPTM Design and Installation Guide 8 4 DET 767A 8 8 ...
Page 123: ...Warnings and Alarms AF 650 GPTM Design and Installation Guide 10 10 DET 767A 10 0 ...
Page 127: ...Basic Troubleshooting AF 650 GPTM Design and Installation Guide 11 4 DET 767A 11 1 ...
Page 129: ...Terminal and Applicable Wir AF 650 GPTM Design and Installation Guide 12 2 DET 767A 12 2 ...
Page 161: ...Specifications AF 650 GPTM Design and Installation Guide 13 32 DET 767A 13 3 ...