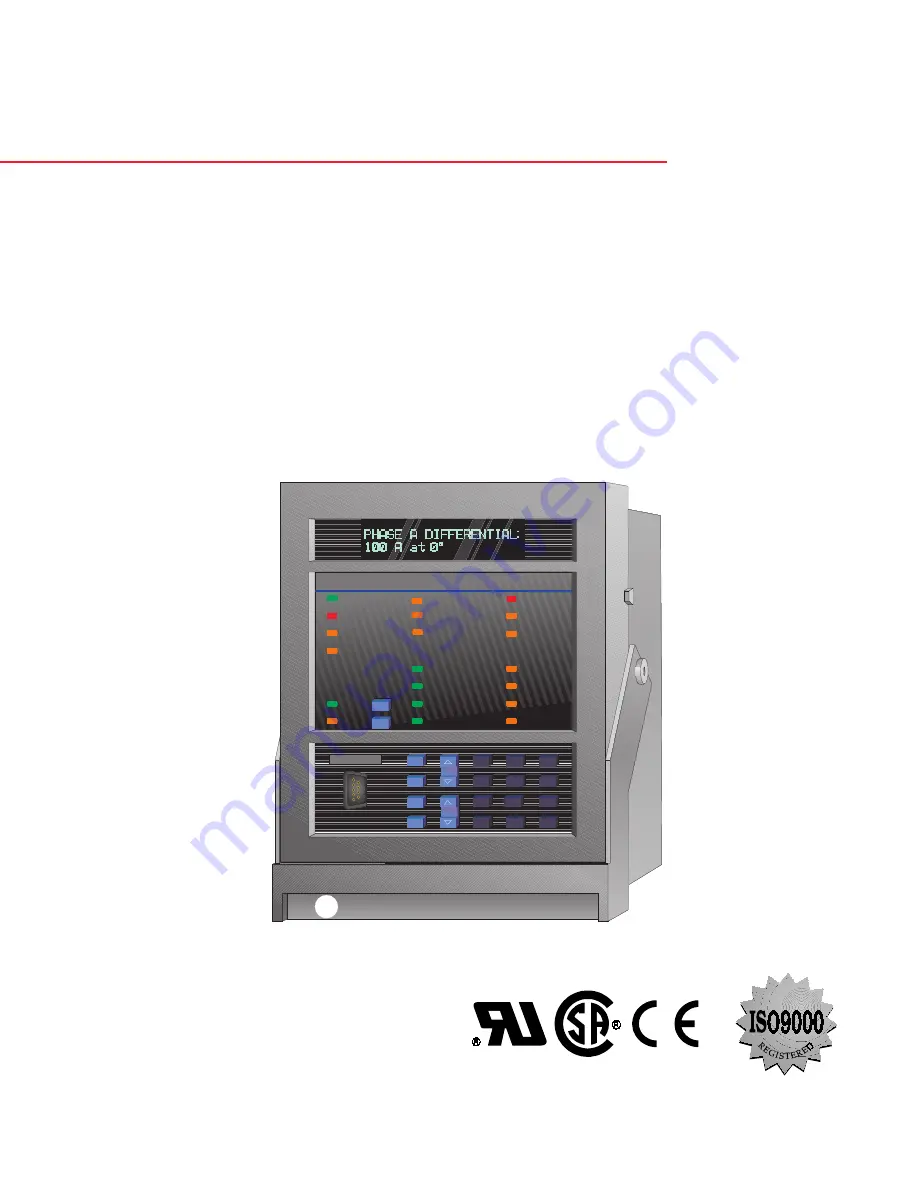
745
TRANSFORMER MANAGEMENT RELAY™
INSTRUCTION MANUAL
Firmware Revision: 250.000
Manual P/N: 1601-0070-B2 (GEK-106292)
Copyright © 2001 GE Power Management
GE Power Management
215 Anderson Avenue, Markham, Ontario
Canada L6E 1B3
Tel: (905) 294-6222 Fax: (905) 294-8512
Internet: http://www.GEindustrial.com/pm
Manufactured under an
ISO9001 Registered system.
g
GE Power Management
745
Transformer Management Relay
™
814768AF.CDR
IN SERVICE
LOCAL
SETPOINT GROUP 2
LOAD-LIMIT
REDUCED
TRIP
SELF-TEST
ERROR
SETPOINT GROUP 3
TRANSFORMER
DE-ENERGIZED
ALARM
PICKUP
TEST MODE
TRANSFORMER
OVERLOAD
SETPOINT GROUP 1
PHASE A
PHASE B
PHASE C
GROUND
MESSAGE
PROGRAM PORT
SETPOINT
7
8
9
4
5
6
1
2
3
.
0
HELP
MESSAGE
VALUE
ACTUAL
ESCAPE
ENTER
RESET
NEXT
DIFFERENTIAL
BLOCKED
745 STATUS
SYSTEM STATUS
CONDITIONS
SETPOINT GROUP 4
g
Summary of Contents for 745 TRANSFORMER MANAGEMENT RELAY
Page 30: ...2 8 745 Transformer Management Relay GE Power Management 2 3 SECURITY 2 GETTING STARTED 2 ...
Page 210: ...7 36 745 Transformer Management Relay GE Power Management 7 2 BLOCK DIAGRAMS 7 SCHEME LOGIC 7 ...
Page 322: ...9 12 745 Transformer Management Relay GE Power Management 9 3 USING 745PC 9 745 PC SOFTWARE 9 ...
Page 396: ...A 4 745 Transformer Management Relay GE Power Management A 1 FIGURES AND TABLES APPENDIXA A ...
Page 400: ...C 2 745 Transformer Management Relay GE Power Management C 1 WARRANTY INFORMATION APPENDIXC C ...
Page 406: ...vi 745 Transformer Management Relay GE Power Management ...
Page 407: ...GE Power Management 745 Transformer Management Relay NOTES ...