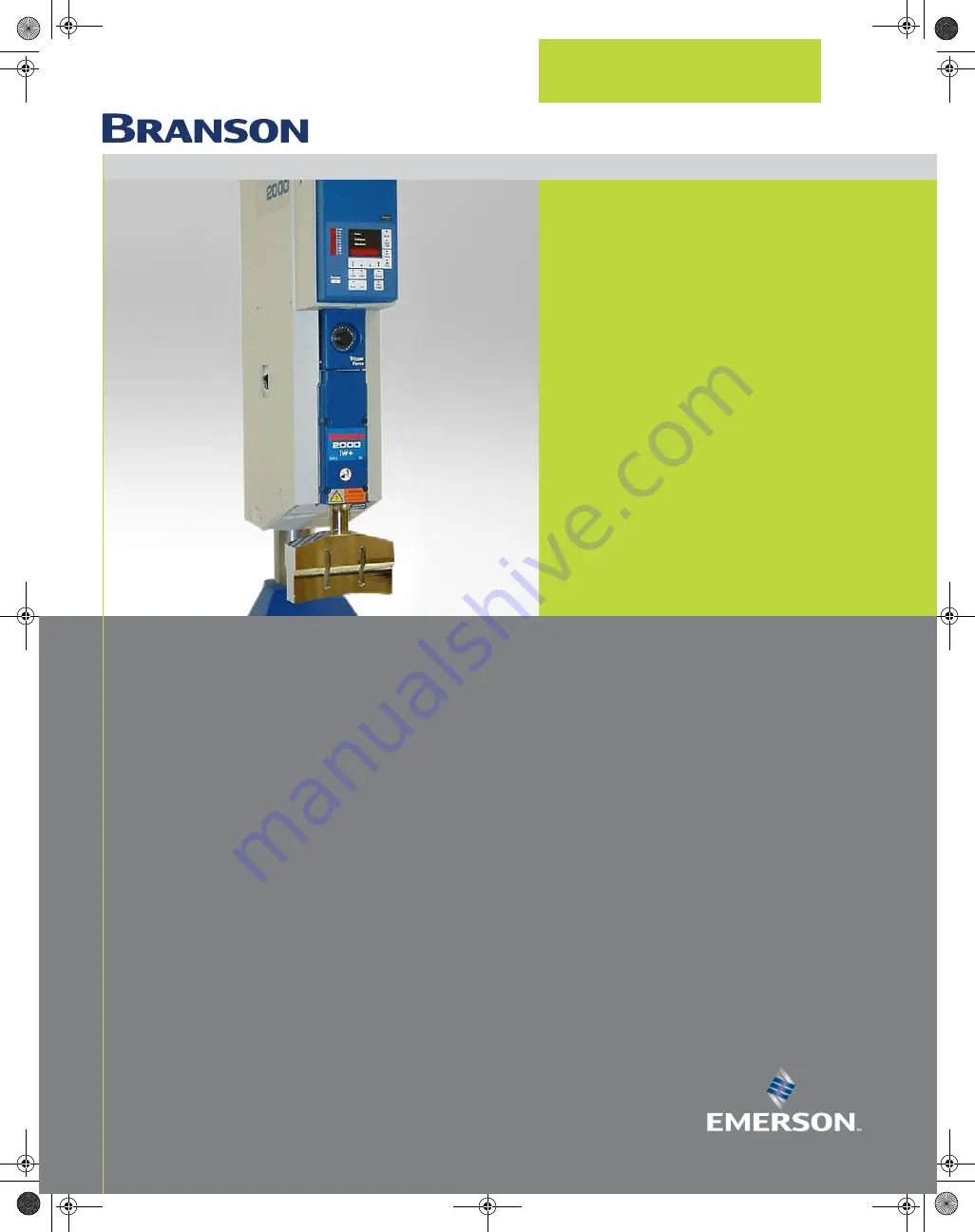
2000IW/IW+
Integrated Welder
Branson Ultrasonics Corporation
41 Eagle Road
Danbury, CT 06813-1961 USA
(203) 796-0400
http://www.bransonultrasonics.com
100-214-251 - REV. 05
I n s t r u c t i o n M a n u a l
100-214-251 IWoper.book Page i Friday, June 16, 2017 4:12 PM
Summary of Contents for Branson 2000 Series
Page 9: ...viii 100 214 251 REV 05 100 214 251 IWoper book Page viii Friday June 16 2017 4 12 PM ...
Page 47: ...38 100 214 251 REV 05 100 214 251 IWoper book Page 38 Friday June 16 2017 4 12 PM ...
Page 83: ...74 100 214 251 REV 05 100 214 251 IWoper book Page 74 Friday June 16 2017 4 12 PM ...
Page 89: ...80 100 214 251 REV 05 100 214 251 IWoper book Page 80 Friday June 16 2017 4 12 PM ...
Page 129: ...120 100 214 251 REV 05 100 214 251 IWoper book Page 120 Friday June 16 2017 4 12 PM ...
Page 135: ...126 100 214 251 REV 05 100 214 251 IWoper book Page 126 Friday June 16 2017 4 12 PM ...