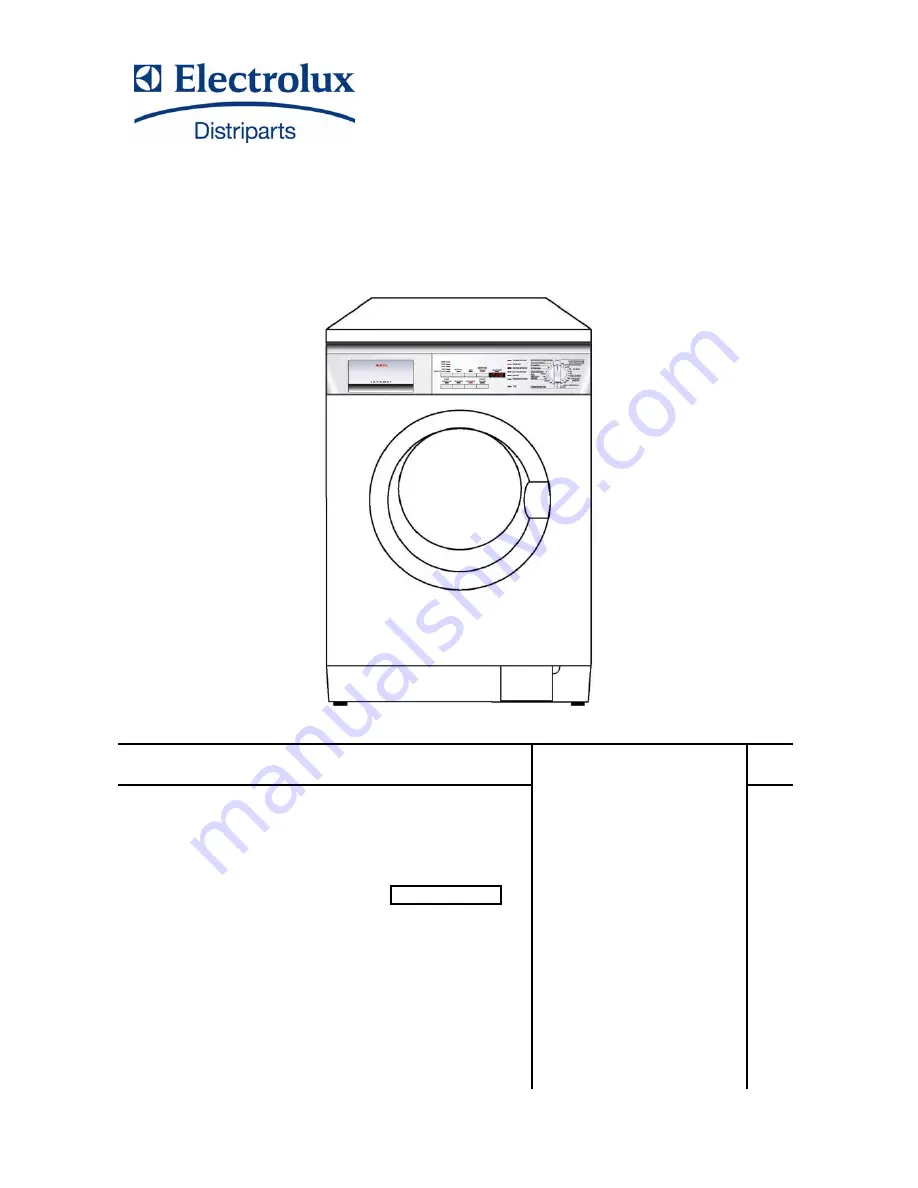
SERVICE MANUAL
WASHING
ELECTROLUX HOME PRODUCTS
ITALY S.p.A.
Spares Operations Italy
Corso Lino Zanussi, 30
Publication no.
I - 33080 PORCIA /PN
599 36 82-56
Fax +39 0434 394096
Edition: 2005-01-12
EN
WASHING MACHINES
&
WASHER-DRYERS
with
EWM2000EVO
Electronic control
With sensors
and
“AEG NEXXXT”
display board
Production ZP (Porcia-Italy)